The Evolution of Distribution Warehouses: Leveraging Technology for Efficient Operations
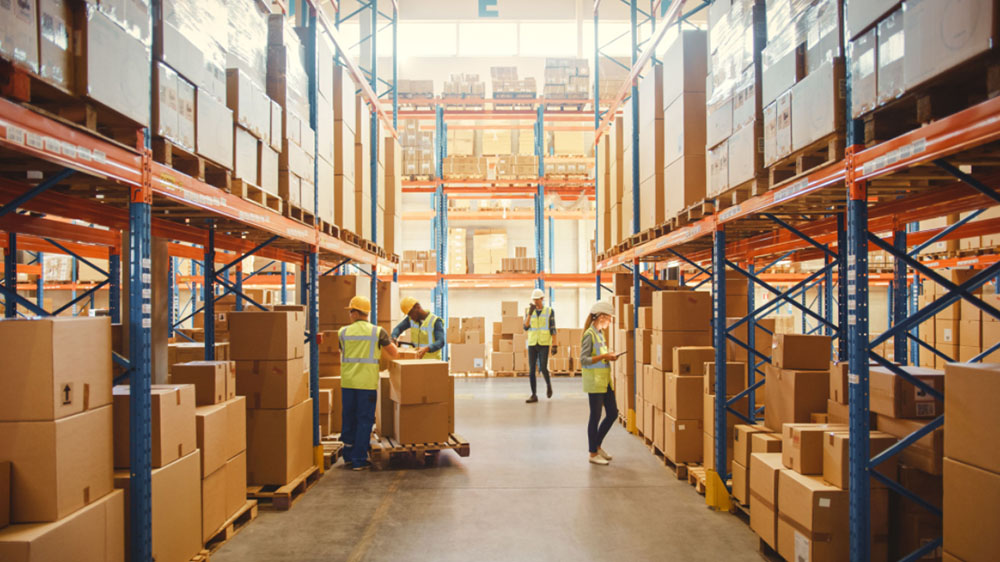
With the rapid advancement of technology, distribution warehouses are undergoing a revolutionary transformation.
In the past, these warehouses relied heavily on manual operations and traditional logistics processes.
However, today, advanced technologies are reshaping the industry. From automated systems to the application of the Internet of Things (IoT), the warehousing sector is actively harnessing the power of technology for efficient operations.
This article explores the significance of distribution warehouses, the role of technology in enhancing their operations, challenges faced by traditional warehousing, and best practices for efficient warehouse management.
A distribution warehouse is a central facility where goods are stored and managed before they are dispatched to retail stores, wholesalers, or directly to customers. It serves as an intermediate point in the supply chain, ensuring the timely delivery of products to their intended destinations.
Distribution warehouses handle tasks such as receiving and storing inventory, order picking and packing, and shipping goods to meet customer demand. These warehouses are designed to efficiently manage large volumes of goods, facilitate inventory tracking, and enable seamless order fulfillment.
Distribution warehouses come in various forms, including public warehouses that provide storage and distribution services for multiple businesses, private warehouses owned by individual companies, and fulfillment centers that focus on e-commerce order processing and shipping.
The size and operations of distribution warehouses can vary widely, depending on the nature of the business and the volume of goods being handled.
Efficient inventory management
Technology enables real-time tracking and monitoring of inventory levels, ensuring accurate stock counts and reducing the risk of stockouts or overstocking.
Automated systems can track product movement, expiration dates, and storage conditions, enabling efficient replenishment and minimizing wastage. By implementing inventory management software and using technologies like barcode scanning and RFID tags, warehouses can streamline the receiving, storage, and retrieval of products, ensuring efficient inventory management.
In addition, advanced software solutions provide comprehensive visibility into inventory data, enabling warehouse managers to make informed decisions regarding stock replenishment, demand forecasting, and storage optimization. By leveraging technology, distribution warehouses can minimize carrying costs, reduce inventory obsolescence, and enhance overall operational efficiency.
Improved order fulfillment
Advanced technologies like barcode scanning, RFID (Radio Frequency Identification), and automated conveyor systems expedite the order fulfillment process.
These technologies streamline picking and packing operations, reducing errors, increasing order accuracy, and improving overall customer satisfaction.
Warehouse personnel can quickly locate products, scan them for accurate picking, and use automated sorting systems for efficient order consolidation and packaging. This enhances speed and precision in fulfilling customer orders, resulting in improved service levels.
Decreased costs and waste minimization
Technology-driven solutions help optimize warehouse layouts, enabling efficient use of space and reducing operational costs.
Automation and robotics can streamline repetitive tasks, reducing labor requirements and increasing productivity. Real-time data and analytics enable accurate demand forecasting, minimizing overstocking and preventing unnecessary wastage.
Traditional warehousing methods often face challenges that can hinder operational efficiency and customer satisfaction:
Inefficient inventory management
Manual inventory tracking can lead to inaccuracies, resulting in stockouts or overstocking, leading to increased holding costs and potential lost sales. Inadequate visibility into inventory levels can also hinder timely replenishment, causing delays in fulfilling customer orders.
Slow order fulfillment
Manual order processing and paper-based systems can be time-consuming and prone to errors, leading to delays in order fulfillment and dissatisfied customers. Inefficient picking and packing processes, coupled with a lack of real-time visibility, can result in delayed shipments and missed delivery deadlines.
Lack of visibility and control
To overcome the challenges mentioned above and optimize warehouse operations, several best practices should be adopted:
Implement a Warehouse Management System (WMS)
DIDADI’s WMS
A WMS automates and streamlines various warehouse processes, including inventory management, order fulfillment, and tracking. It provides real-time visibility into inventory levels, improves accuracy, and enhances operational efficiency.
A WMS allows for efficient management of receiving, put-away, picking, packing, and shipping processes, enabling better control and increased productivity.
Utilize inventory management software
Implementing specialized inventory management software enables effective tracking, organizing, and optimizing of inventory levels. It helps minimize stockouts, reduce excess inventory, and improve overall inventory accuracy. The software can generate real-time reports and analytics, enabling informed decision-making regarding inventory replenishment, demand forecasting, and storage optimization.
Regular reporting and tracking of key performance indicators (KPIs) such as inventory turnover, order fulfillment rate, and warehouse capacity utilization help identify areas for improvement and drive operational efficiency. By continuously monitoring these metrics, warehouses can identify bottlenecks, streamline processes, and enhance overall performance.
Adopting a culture of continuous improvement and data-driven decision-making enables distribution warehouses to optimize their operations continually.
Regular tracking and reporting of KPIs not only highlight areas requiring attention but also help identify opportunities for efficiency gains and cost savings. By leveraging data analytics, warehouses can uncover trends, predict demand fluctuations, and optimize resource allocation for improved operational performance.
DIDADI offers comprehensive fulfillment services that combine cutting-edge technology, streamlined processes, and expertise to optimize distribution warehouses. With our advanced inventory management systems, automated order fulfillment processes, and real-time analytics, DIDADI helps businesses achieve seamless warehouse operations, enhance customer satisfaction, and drive business growth.
Our fulfillment services encompass a range of activities, including inventory storage and management, order processing, packaging, and shipping. By leveraging the latest technologies and best practices, DIDADI ensures efficient and cost-effective warehousing and fulfillment solutions for businesses of all sizes.
Distribution warehouses are undergoing a significant transformation fueled by advancements in technology. By embracing these technological innovations, distribution warehouses can optimize their inventory management, streamline order fulfillment processes, and reduce costs.
Implementing best practices such as adopting a WarehouseManagement System (WMS), utilizing inventory management software, and tracking key performance indicators are essential for improving warehouse operations. The integration of technology and automation allows for real-time visibility, enhanced productivity, and better control over inventory and order fulfillment.
Recommended Reading
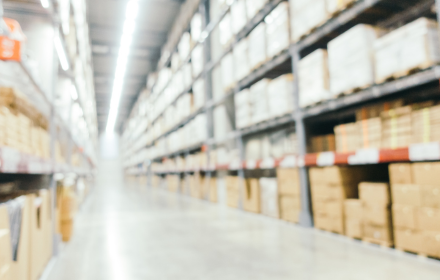
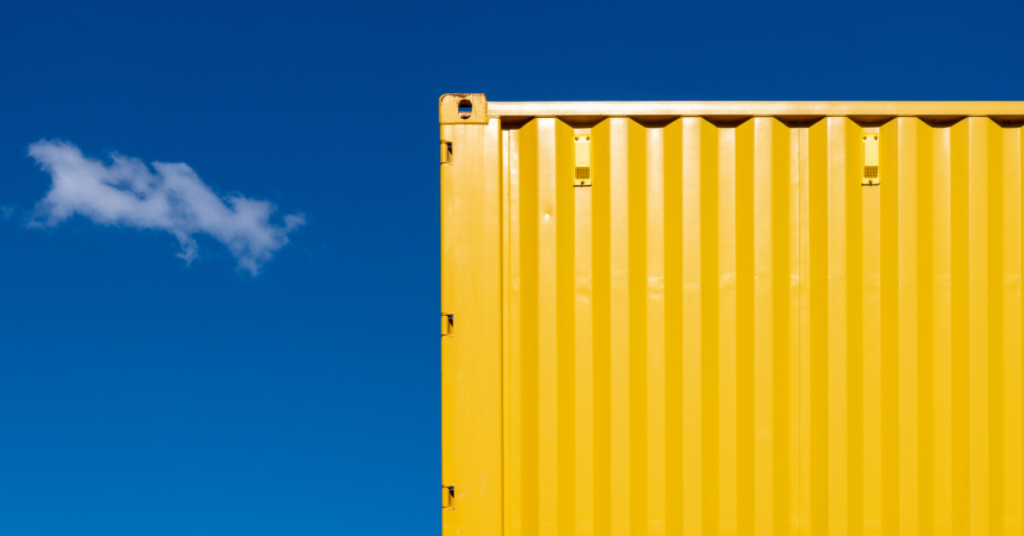
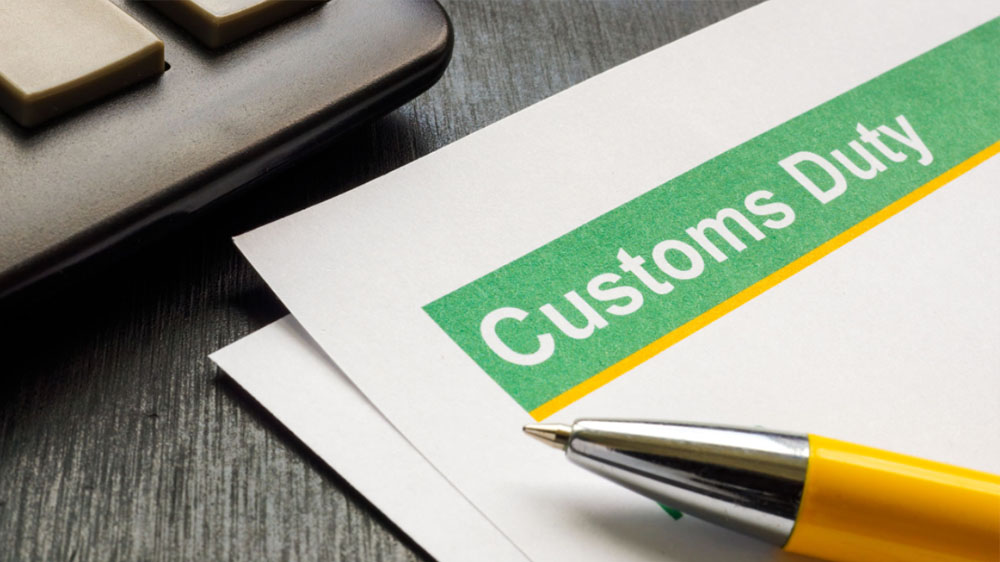
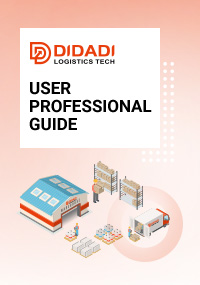